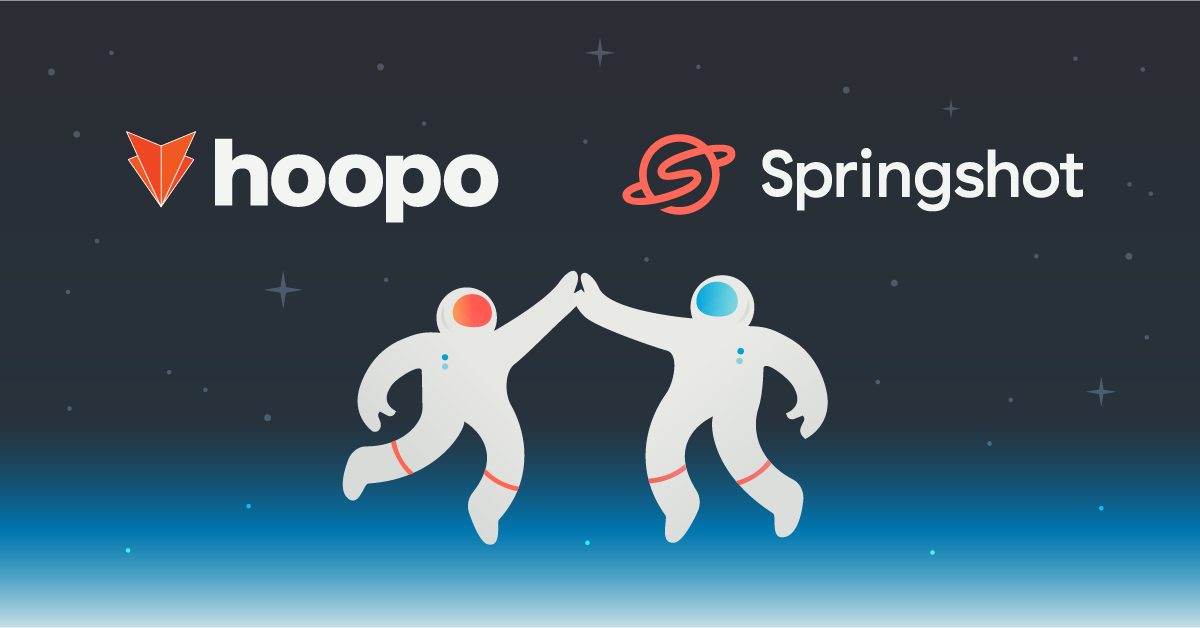
In today’s fast-paced and resource-strained airport environment, the need for smarter, more efficient management of Ground Support Equipment (GSE) is paramount. This is where the partnership between Springshot and Hoopo has truly come to life, creating a synergy that is reshaping asset management in airport operations. Since the integration of Hoopo’s real-time tracking technology with Springshot’s platform, a new era of efficiency, accountability and innovation has begun. We are excited to share the successes of 2024, highlight the remarkable strides made and look ahead to the possibilities of 2025.
The Challenge: Managing Thousands of Assets
Airports worldwide face the ongoing challenge of managing extensive fleets of non-motorized GSE – ranging from baggage carts to ULD (unit load device) dollies – across sprawling terminals and cargo warehouses. These assets are critical to airport operations but are often difficult to track and control. Misplaced or underused equipment leads to unnecessary operational delays and, in many cases, costly purchases of new assets. This inefficiency is exacerbated by the manual processes that ground handling staff traditionally rely on to monitor equipment usage and location.
For one major airline partner, managing a diverse customer list – ranging from cargo to passenger airlines – across multiple terminals and warehouses was a labor-intensive task. Employees would spend 15 to 45 minutes per flight simply tracking and controlling GSE. The result? Equipment was often misplaced or left idle, leading to increased manual labor and unnecessary GSE purchases.
The Solution: Real-Time Tracking with Hoopo and Springshot
In response to this challenge, Springshot and Hoopo collaborated to bring a revolutionary solution to the table. By integrating Hoopo’s telemetry system into Springshot’s user-friendly platform, we’ve equipped ramp service teams with the real-time information they need to maximize GSE utilization and minimize downtime.
This integration allows personnel to see exactly where each piece of equipment is located across the airport campus. With the use of geofencing, ramp agents can now track assets within specific zones, such as cargo warehouses, ensuring that no equipment is left unaccounted for. Moreover, through load sensing technology activated on the ULD dollies, the system can show whether the equipment is occupied (i.e., carrying a ULD) or not, providing a clear, real-time view of asset availability.
This integration has unlocked new levels of efficiency. Springshot’s real-time data shows exactly where all the equipment is at any given moment; whether it’s being used, in maintenance or simply sitting idle. Ground handlers can easily locate and deploy equipment, reducing wasted time and manpower.
Scaling Up: Over One Thousand Sensors Deployed
In 2024, thousands of trackers were successfully deployed across several major airports spanning multiple continents to track non-motorized GSE. This extensive deployment included baggage carts and ULD pallet dollies, which are now tracked in real-time via the Springshot platform.
The results have been dramatic. Ramp staff no longer have to search for missing equipment, wasting precious time. Instead, they can pull up a map on the Springshot interface and immediately see where each piece of equipment is located and whether it is available for use. This increased visibility has proven to be especially useful in cargo operations, where the ability to see where built-up transfer ULDs are staged across the ramp means that staff can quickly move them to the correct flight, eliminating unnecessary delays and increasing operational efficiency.
For cargo operations, the real-time location of assets has been a game-changer. Geofencing allows frontline personnel to track whether built-up ULDs and dollies are inside a warehouse or out on the ramp, giving them a clear picture of availability and status when timeliness and accuracy really matter.
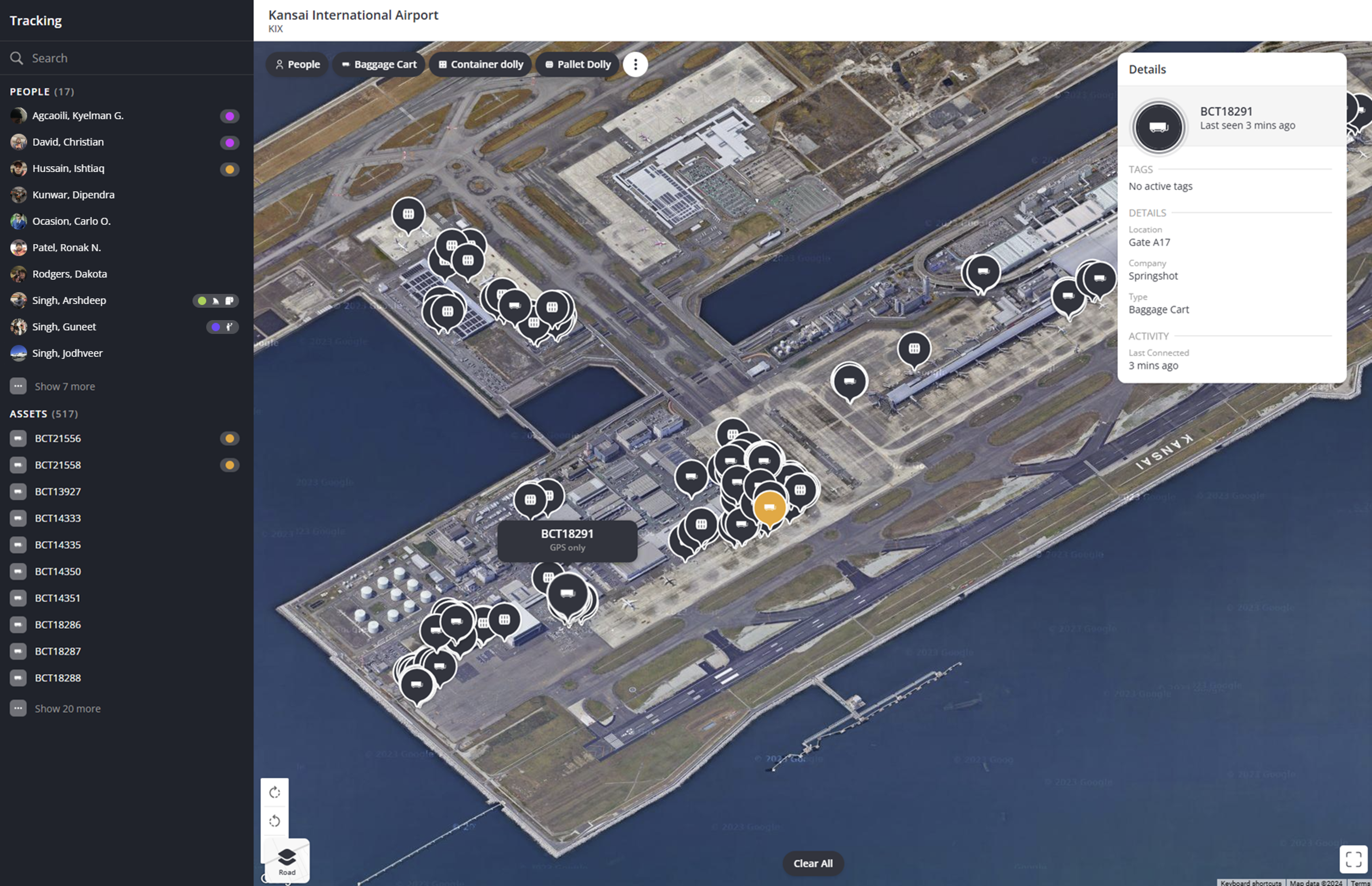
Streamlining Operations: Visibility, Accountability and Transparency
The key to this integration is not just location tracking, but the ability to see exactly when, where and how equipment is being used. This insight fosters accountability on both sides (staff and management) and provides a data-driven approach to operations. Ground service teams can now easily identify underutilized equipment, ensuring that no assets are left idle for long periods.
The system also enables airlines and ground handlers to share resources seamlessly across operations. If one airline’s equipment is being overused, another can offer resources to ensure smooth operations across the board. With real-time access to data, decision-making is based on facts, not guesswork. This has led to better coordination, more efficient use of equipment and the ability to quickly address operational bottlenecks.
“For ground handlers, having one platform that addresses both workforce and asset management is transformative,” said Tal Leemor, VP of marketing and partnerships at Hoopo. “This collaboration provides ground handlers with real-time visibility and actionable insights, empowering them to operate more efficiently while reducing wasted resources and maximizing value.”
Looking Ahead: 2025 and Beyond
As we reflect on the tremendous progress made in 2024, both Springshot and Hoopo are excited about the future. The technology now in place has proven to be transformative, but there is still so much potential for growth in 2025. In the coming year, we aim to expand the reach of this tracking system, adding more trackers, enhancing geofencing capabilities and exploring predictive analytics to further improve asset management and resource allocation.
With the foundation already set, the path forward is clear: we will continue to build on our successes, refine the system and introduce new innovations that will drive further efficiencies in ground operations. As Doug Kreuzkamp, Founder and CEO of Springhsot, notes: “Given plummeting global birthrates and anticipated labor scarcity due to nativist geopolitics, it’s never been more important to augment the mental and physical capacities of each human worker. We’re proud of the work we’re doing with Hoopo to upskill airport workers around the world. By making it easier and more efficient for them to track, utilize and manage large fleets of GSE, we’re empowering them and our customers to do more with less.” The collaboration between Springshot and Hoopo is just beginning, and we can’t wait to see how this partnership will continue to evolve in the years ahead.
A Future of Smarter Operations
The partnership between Springshot and Hoopo represents a significant step forward in the optimization of airport operations. Together, we have created a solution that not only improves the visibility and utilization of GSE, but also lays the groundwork for a more efficient, data-driven future in aviation. As we look toward 2025, we are energized by the possibilities that lie ahead and the continued success of this collaboration.
Stay tuned because the best is yet to come.